فهرست مطالب
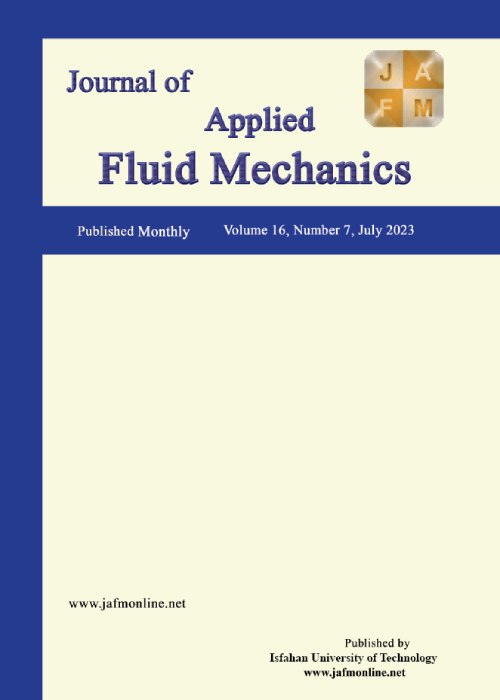
Journal Of Applied Fluid Mechanics
Volume:16 Issue: 9, Sep 2023
- تاریخ انتشار: 1402/04/14
- تعداد عناوین: 15
-
-
Pages 1704-1716This paper proposes a novel design for a hybrid engine air-particle separator filter (HEAPS) that combines the vortex tube separator (VTS) with the inertial particle separator (IPS) to enhance separation efficiency. Helicopters often operate in harsh environments, such as deserts, and landing on unprepared runways poses a severe risk to turboshaft engines due to the ingestion of dust and sand. This can result in significant damage to the engine's rotating components, impacting its life, reliability, and performance. To protect the engine from erosion and damage, an engine air particle separator system (EAPS) is installed in the engine inlet. In this study, a comparative numerical simulation was conducted between the hybrid filter and the VTS using the commercial software ANSYS Fluent. The Reynolds-averaged Navier–Stokes equations (RANS) were used to simulate incompressible turbulent flow, and the trajectory of particles was tracked using the Discrete Phase Model (DPM). Particle trajectories and separation efficiency were analyzed for different particle sizes, inlet velocities, and bypass mass flow ratios between the scavenge channel and the core engine channel. The results show that the hybrid design provides excellent separation efficiency, with a recovery efficiency of over 97%.Keywords: Innovative hybrid filter geometry, Vortex tube separator, Inertial particle separator, Separation efficiency, Discret phase model
-
Pages 1717-1728In this study, the flow boiling heat transfer and pressure drop characteristics of refrigerant R134a in micro-channels were experimentally investigated. The tests were performed in circular horizontal micro-channels with inner diameters of 0.5 mm and 1 mm and a heating length of 300 mm. The mass velocities varied from 500 kg/m2s to 2500 kg/m2s, and the heat fluxes varied from 15 kW/m2 to 147 kW/m2. The heat transfer coefficient (HTC) and frictional pressure drop (FPD) were measured and discussed in detail. According to the results, HTC was significantly affected by heat flux, whereas it was independent of mass velocity. Nucleate boiling was the dominant heat transfer mechanism for R134a flow boiling in the micro-channels. In comparison to the 1 mm channel, the 0.5 mm channel shows better performance in heat transfer, with a maximum increase of approximately 22 %. In addition, FPD increased with increasing mass velocity and decreasing channel diameter. Finally, several existing correlations for HTC and FPD were evaluated by comparing them with the experimental values. Tran’s correlation (1996) presented a better agreement in terms of the average HTC, while for the FPD, the model of Kim and Mudawar (2013b) showed good prediction accuracy.Keywords: Micro-channel, Flow Boiling, Heat transfer, Frictional pressure drop, Predictive correlations
-
Pages 1729-1741When reducing the energy prerequisites of buildings, the correct distribution of fresh air flows injected into the living rooms poses a problem. If the problem of mixing the injected air in the ambient air is not effectively solved, there will be a strong deterioration in air quality and comfort. In this research, a new design of swirling diffuser is investigated experimentally and numerically using large eddy simulations. The influence of fins is studied for the improvement of air diffusion and jet mixing with ambient air. The study was carried out for a fins angle of 30° with the jet's axis and 60° with the blowing orifice's plane with the condition of uniform heat flux of the air. The working fluid used is air. It has been validated that using fins leads to a greater spreading of the jet and good air mixing compared to those obtained from smooth tubes (circular nozzle). To enhance the accuracy of the turbulence models' predictions, three turbulence models are tested: the wall-adapting local eddy-viscosity turbulence model (LES/WALEVM), Smagorinski-Lilly (LES/S-LM) model and the kinetic-energy transport model (LES/K-ETM). It is worth highlighting that the LES/K-ETM model is well established in the prediction of swirling flows, which have been successfully compared with experimental results.Keywords: Swirl diffusers, Large eddy simulation, Indoor air quality, CFD, Turbulence models
-
Pages 1742-1751In this study, a dynamic mixer was designed to mix polymer melts online during extrusion, and the flow of a polymer melt in a mixer was simulated using Polyflow software. The Orthogonal experiment was conducted to analyze the effects of three geometrical parameters (i.e. the length of entrance zone (Li), the gap between the rotor and wall (g), and the diameter of cone-shaped rotor (d2)) on mixing properties of a dynamic mixer. The Li, g, and d2 were optimized for the minimum product of segregation scale (S) and power consumption (P). Finally, the mixing properties of the dynamic mixer were compared with those of SK and SX static mixers. The results indicated that among the above-mentioned three parameters, the g was the most important parameter influencing S, and S∙P. The minimum S∙P of 1059 µm·W was obtained when the Li was 16 mm, the g was 1 mm, and the d2 was 24 mm. The S decreased with the increase of the rotation speed from 120 to 360 r/min, and increased with the increase of the flow rate from 15 to 45 mL/min. However, the P increased with the increase of both the rotation speed and flow rate. The maximum shear rate of the melt in the dynamic mixer was observed in the mixing zone, which was mainly affected by the rotation speed rather than the flow rate. To achieve the S of the same size, the length of the dynamic mixer was the shortest, and that of the SK static mixer was the longest. Moreover, to acquire the S of the same size, the dynamic mixer required the largest P, the SX static mixer needed a smaller P, and the SK static mixer required the minimum P.Keywords: mixer, Numerical simulation, Parameter optimization, Power consumption, Segregation scale
-
Pages 1752-1766In order to upsurge the maneuverability of micro aerial vehicles, a tubercle leading edge inspired by the whale flipper was applied as a passive stall control method. Although this method could be useful to control stall phenomena, the effect of geometrical properties on the flow physic should be investigated to reach the root of them. According to preceding research, the effect of some parameters on the tubercle leading edge wing is a hot topic among researchers. The aim of this research is to explore the effects of sectional wing geometries like amplitude, wavelength, thickness, maximum thickness location, and camber on the aerodynamic feature of full-span tubercle leading edge wing, particularly at 22 degree in post-stall circumstances. The results present that by reducing the amplitude about 2.5%c, the lift coefficient upsurges by about 3.5%; instead, the drag coefficient reduces about 6%. On the other hand, by decreasing the wavelength from 46.2%c to 11.7%c, the drag coefficient and the lift coefficient decrease by about 15% and 19%, respectively. Furthermore, as the thickness rises from 10.55%c to 18.14%c, the lift and drag coefficient goes down about 9.4% and 2.9%, respectively. Furthermore, by increasing the camber from 2.56%c to 3.34%c, the lift to drag ratio goes down by about 1.06%. Finally, by raising the last design variable (maximum thickness location) from 0.26c to 0.51c, the lift to drag ratio increases about 13.7%.Keywords: Full-span tubercle leading edge wing geometrical parameters, Flow Separation Area (FSA), Air dry zone aerodynamic forces, Power Spectral Density (PSD), Fast Fourier Transform (FFT)
-
Pages 1767-1777
Secondary flow is a prominent feature of channel bends; it alters the streamwise velocity and bed shear stress distributions. Experiments were conducted to investigate the complex pattern of secondary flow in a narrow and sharp open-channel bend and the underlying mechanism of generation of multiple circulation cells. Compared with the moderate bends, the sharp bends are characteristic of multiple circulation cells from the 90° section. In addition to the curvature-induced circulation cell (S1) and turbulence-induced counter-rotation circulation cell (C1) near the outer bank, another circulation cell (S2) was observed near the inner bank and was attributed to flow separation. A term-by-term analysis of the vorticity equations indicates that the centrifugal term favours S1 and C1 while opposing S2. The turbulence-related term accounts for the formation of C1 and S2. The advective transport term redistributes vorticity and maintains the existence of S2. The dependence of secondary flow structure on Reynolds number and aspect ratio was also explored. With an increase in the Reynolds number from 23000 to 37000, both the strength and size of C1 are reduced by 50%, whereas the size of S2 increases by 20%, and its strength slightly decreases. With a decrease in the aspect ratio from 3.3 to 2, the strengths of S1, S2, and C1 are doubled, and the sizes of C1 and S2 increase by 90% and 20%, respectively.
Keywords: Secondary flow, Vorticity transport equations, Open-channel bends, Aspect ratio, Reynolds number -
Pages 1778-1791The hydrodynamic behaviour of air-glass beads bubbling fluidized bed reactor containing spherical glass beads is numerically studied, using OpenFoam v7 CFD software. Both Gidaspow and Syamlal-O'Brien drag models are used to calculate momentum exchange coefficients. Simulation predictions of pressure loss, bed expansion rate, and air volume fraction parameters were compared and validated using data, existing in the literature obtained experimentally and performed by other numerical softwares. Pressure loss and rate of bed expansion were calculated with relative root mean square error (RMSE) equal to 0.65 and 0.095 respectively; Syamlal-O'Brien model is considered more accurate than Gidaspow model. Hence, numerical model reliability developed on OpenFoam was also proved. The hydrodynamic aspect study of the fluidized bed reactor was then performed, to analyse the impact of inlet air velocity (U) on particles motion. It was revealed that with U increment, air and glass beads axial velocities increase in the reactor centre and decrease in the sidewalls. Thus, a greater particle bed expansion is induced and the solid particles accumulated highly on the reactor sidewalls. In general, with the increase of U, the solid volume fraction decreases from 0.63 to 0.58 observed at 0.065 m/s and 0.51 m/s, respectively.Keywords: CFD modelling, Eulerian-Eulerian approach, Fluidized bed reactor, Hydrodynamic, Multiphase flow, OpenFOAM
-
Pages 1792-1805In addition to noise and vibration, cavitation also lowers the efficiency, performance, and working lives of two-dimensional valves. To study the effect of cavitation on the flow characteristics of two-dimensional valves, standard turbulence model and an energy equation model were selected, and the local entropy production rate was defined using the custom field function. The entropy production theory was introduced to numerically simulate the cavitation flow in a two-dimensional valve, and based on this, the structure of the pilot stage of the valve was optimized. The results showed that there was a distinct correlation between the entropy production and the flow characteristics of the valve. When the mass flow rate changed, the entropy production also changed. The turbulent dissipation entropy production always accounted for more than 50% of the total entropy production in the flow field. In the valve sleeve chute area downstream of the valve throttling port, turbulence dissipation entropy production was concentrated; and the energy loss was large. According to the optimization of the structure of this area, the total entropy production of the side-V-slot valve sleeve structure was 7.46% lower than that of the unslotted valve sleeve structure for different valve openings, while the total entropy production of the rear-V-slot valve sleeve structure was 14.31% higher. The energy loss caused by cavitation could be better reduced using a V-shaped groove on the side of the valve sleeve.Keywords: Two-dimensional valve, Turbulent dissipation entropy production, Cavitation, Suppression, Computational fluid dynamics
-
Pages 1806-1817The continuous demand and fuel depletion in the automobile industries cause a reduction in fuel consumption, especially in a car which is a classic problem to focus on vehicle body design. The formation of drag force in the car body demands tractive force and significantly affects the engine performance and fuel consumption rate which is not advisable for enhancing aerodynamic efficiency. This paper discusses the methodology to reduce the fuel consumption rate in hatchback cars using a ‘basebleed method’. The hatchback car model with and without basebleed is numerically simulated for the various speed to study the aerodynamic coefficients. The numerical simulation is performed with the k-ε turbulence model for predicting the wake region of both car models with and without basebleed. The numerical study witnessed the hatchback car model with basebleed arrived 6% reduction in the coefficient of drag (CD) compared to without basebleed, which results in a reduction of fuel consumption rate of up to 4.33 %. The research evidence that the stability of the car is not affected while using this basebleed drag reduction method and it is studied from the resultant parameters such as coefficient of lift (CL) and coefficient of side force (CS) and for the varying yaw angle (φ). Further, the research recommends the integration of basebleed at the underbody structure in Hatchback cars to improve the engine fuel consumption without affecting its stability.Keywords: Hatchback car, Vehicle design, CFD, Drag force, Fuel consumption
-
Pages 1818-1827Ingestion and deposition of fine particles on the surface of the coolant passage degrade the blade’s cooling performance. This paper proposes a deposition model to investigate the complex deposition characteristics of fine particles during repeated collision, adhesion, rebound, and removal events in the small space inside a typical impingement-effusion structure with a double-wall blade. The results show that the particles rarely collide with the wall and escape directly from the film hole outlet when the particle diameters are smaller than 0.5 μm. Most particles with diameters of 0.5 to 1.0 μm are deposited after the first collision around the stagnation point in an area 0.35 times the pin-fin diameter. Some particles with diameters of 1.0 to 3.0 μm are deposited in the stagnation region, but most are deposited between the two pin fins and near the film hole after the second collision. Particles with diameters larger than 3.0 μm are mainly deposited on the region enclosed by the adjacent pin fins and film holes after multiple collisions, and the escape rate of particles is higher than 30%. The escape rates of particles with diameters of 0.5 to 1.0 μm and 1.0 to 3.0 μm have the same trends, exhibiting a decrease followed by an increase with the increasing particle diameter. The particles entering the impingement-effusion structure, especially those with diameters of 0.7 -0.8 μm and 1.4 -2.4 μm, are primarily deposited on the target surface, resulting in the cooling performance degradation of double-walled blade.Keywords: Impingement-effusion structure, Deposition model, Particle size, Deposition distribution, Degradation of cooling performance
-
Pages 1828-1838This study examines the effects of temperatures and directions of the magnetic fields in the combustion chambers on flame characteristics for boiler combustion in power generation systems by burning olive oil droplets. The variations in the temperature of the combustion chamber are 40°C, 50°C, and 60°C. Meanwhile, the directions of the magnetic fields are the repulsive magnetic field (north-north) and the attractive magnetic field (north-south). In the experiment, a droplet of olive oil was placed at a type K thermocouple junction between the two bar magnets. A 250 fps high-speed camera recorded the flame from its ignition to its extinction. The results of this study found that temperature and direction of the magnetic fields in the combustion chamber have an effect on the characteristics of the flame, where the attractive magnetic field (north-south) resulted in increased burning of droplets, round flame, low altitude, increased temperature, and shorter ignition delay time, compared to the repulsive magnetic field (north-north) and without a magnetic field. Furthermore, the combustion chamber temperatures of 40°C, 50°C, and 60°C produced flame temperatures of 799.94°C, 829.25°C, and 879.50°C, and flame heights of 5.97 mm, 5.35 mm, and 4.23 mm, respectively. The strong magnetic fields increased the concentration of oxygen and fuel molecules around the combustion reaction zone, causing shorter droplet combustion and releasing a large amount of energy. These findings are beneficial for designing efficient industrial heat generators with a magnetic field. The results of this study are therefore crucial as a basis for considering the substitution of fossil fuels with environmentally friendly vegetable oils.Keywords: Vegetable oil, Magnetic fields, Droplet combustion, Flame characteristics, Flame evolution
-
Pages 1839-1852Compact aero-engines that use centrifugal compressors are in high demand due to their small size and cost-effectiveness. However, limited improvements in the aerodynamic performance of centrifugal impellers have led to a greater focus on improving the performance of diffusers. This paper introduces a novel vane conformal diffuser designed to match an impeller with a high pressure ratio. The diffuser utilizes a unique design method that creates transitions from a two-dimensional meridian to a three-dimensional configuration, to achieve a twisted design for the vane and hub. Eventually an integrated vane configuration is formed from the radial section to the bend and axial sections. The novel diffuser significantly reduces the radial size of the entire compressor compared with a conventional vaned diffuser. Different cross-section area distributions are studied to explore the reasonable static pressure recovery ability of the diffuser. To validate the new concept, the diffusers of two existing high-pressure centrifugal compressors are redesigned using the novel conformal diffuser configuration. The numerical results show that the aerodynamic performances of the two redesigned centrifugal compressors are improved in terms of both the total pressure ratio and the isentropic efficiency compared with their counterparts. These results demonstrate the effectiveness and applicability of the developed design method for the novel conformal diffuser.Keywords: Vaned-twisted, Conformal diffuser, Compact centrifugal compressor, Numerical simulation, Turbomachinery
-
Pages 1853-1864Thermocapillary convection flows can have an impact on the homogeneity of floating zone semiconductor crystals. An external magnetic field can also help to reduce this non-homogeneity. The goal of this research is to minimize thermocapillary convection in various thin annular pools filled with silicon melt. A three-dimensional (3D) numerical technique is proposed that employs an implicit finite volume formulation. The steady-state thermocapillary flow in six thin annular pools (R=0.3, 0.4, 0.5, 0.6, 0.7, and 0.8) subjected to an externally induced magnetic field was observed. Under magnetic field influence, the effects of increasing annular gap, R on the hydrothermal wave number and azimuthal pattern are obtained. The results reveal that hydrothermal waves m=14, m=11, m=8, m=6, m=4, and m=3 are observed in steady flow for R=0.3; 0.4; 0.5; 0.6; 0.7, and R=0.8, respectively. The maximum temperature occurs in the intermediate zone between the inner and outer walls when there is no magnetic field. Under a strong enough magnetic field, isothermal lines change form and become concentric circles. As the amplitude of the magnetic field (Ha) grows, the azimuthal velocity and temperature at the free surface reduce, and the asymmetric 3D flow becomes axisymmetric steady when Ha surpasses a threshold value.Keywords: Thermocapillary convection, hydrothermal wave, Magnetic field, Annular pools, Silicon melt
-
Pages 1865-1876Flow distortions in high-speed inlet systems are complex, and high-performance air-breathing propulsion systems. In this paper, large eddy simulations are performed to study the total pressure and swirl distortions in a Busemann inlet at freestream Mach number 6. The on-design flow condition with both the Attack Angle and Sideslip Angle equal to zero and two off-design conditions (Attack Angle = 6 deg, Sideslip Angle = 0 deg and Attack Angle = 6 deg, Sideslip Angle = 6 deg) are considered to explore the flow characteristics inside the inlet duct as well as the distortions at the inlet exit plane. It is found that under the on-design flow condition, the shock structures and boundary layer development are nearly axisymmetric about the inlet axis. The captured freestream is compressed smoothly through inlet duct. The total pressure loss is limited primarily to within the boundary layer region, and nearly no swirling flow is introduced during the flow compression process. Under the off-design flow conditions, the shock structures inside the inlet duct become non-axisymmetric, and localized strong shock–boundary layer interactions occur. In the case of the off-design flow condition with Attack Angle = 6 deg, Sideslip Angle = 0 deg, a large flow separation zone appears owing to the incidence of a strong curved shock on the wall surface at the leeward side in the inlet duct, and the low-kinetic-energy flow contained in this flow separation zone leads to an obvious total-pressure reduction at the exit plane of inlet. Meanwhile, a large-scale swirling flow is formed at the exit plane of inlet owing to the appearance of a nonuniform transverse pressure gradient. Under the off-design conditions, a pair of vortex is observed at the exit plane of inlet. The shock wave–boundary layer interactions under the off-design conditions are stronger than those under the on-design condition, which results in more intense total pressure and swirl distortions. The averages of the fluctuating distortions are more evident than the temporal-averaged total-pressure and swirl distortions. These results show that turbulent flow fluctuations are important in determining the overall distortion level in a Busemann inlet.Keywords: Hypersonic inlet, Busemann inlet, Large eddy simulation, Total pressure distortion, Swirl distortion, Shock wave–boundary layer interaction
-
Pages 1877-1886Numerous studies have been conducted to investigate effect of blade geometry of vertical axis wind turbine performance. Most of the evaluations have focused on the airfoil series and airfoil geometry parameters such as thickness and camber of the airfoil. Few studies have examined the effect of other blade geometry parameters on the vertical axis wind turbine performance. In the present study, the effect of geometric change in leading-edge radius (LER) of a vertical axis wind turbine performance has been numerically studied. Hence, modified NACA 0021 airfoil profiles were created using the geometric method (CST). Then, the flow behavior around a Darrieus vertical axis wind turbine was simulated under the influence of the reduction and set-up coefficients of the leading-edge radius at a constant wind speed of 9 m/s and a tip speed ratio of 1.5 to 3.5 using the computational fluid dynamics. Additionally, the effects of the examined parameter (leading-edge radius) on fluid flow and aerodynamic performance coefficients, including the coefficients of power and torque, were investigated. The results indicated that the leading-edge radius affected the near wake flow of the turbine, and the optimization of leading-edge radius parameter controls the dynamic stall and reduces the formation of a vortex. Finally, the optimization of LER revealed that at 20% reduction in the LER the performance of the turbine at tip speed ratio of 1.5 was increased by more than 50%. This reinforces the self-starting capability of a Darrieus wind turbine.Keywords: Darrieus wind turbine, Computational fluid dynamics (CFD), Class functions, Shape functions transformation (CST), Dynamic stall, Leading-Edge Radius (LER)